Field Handling Galvanized Rebar
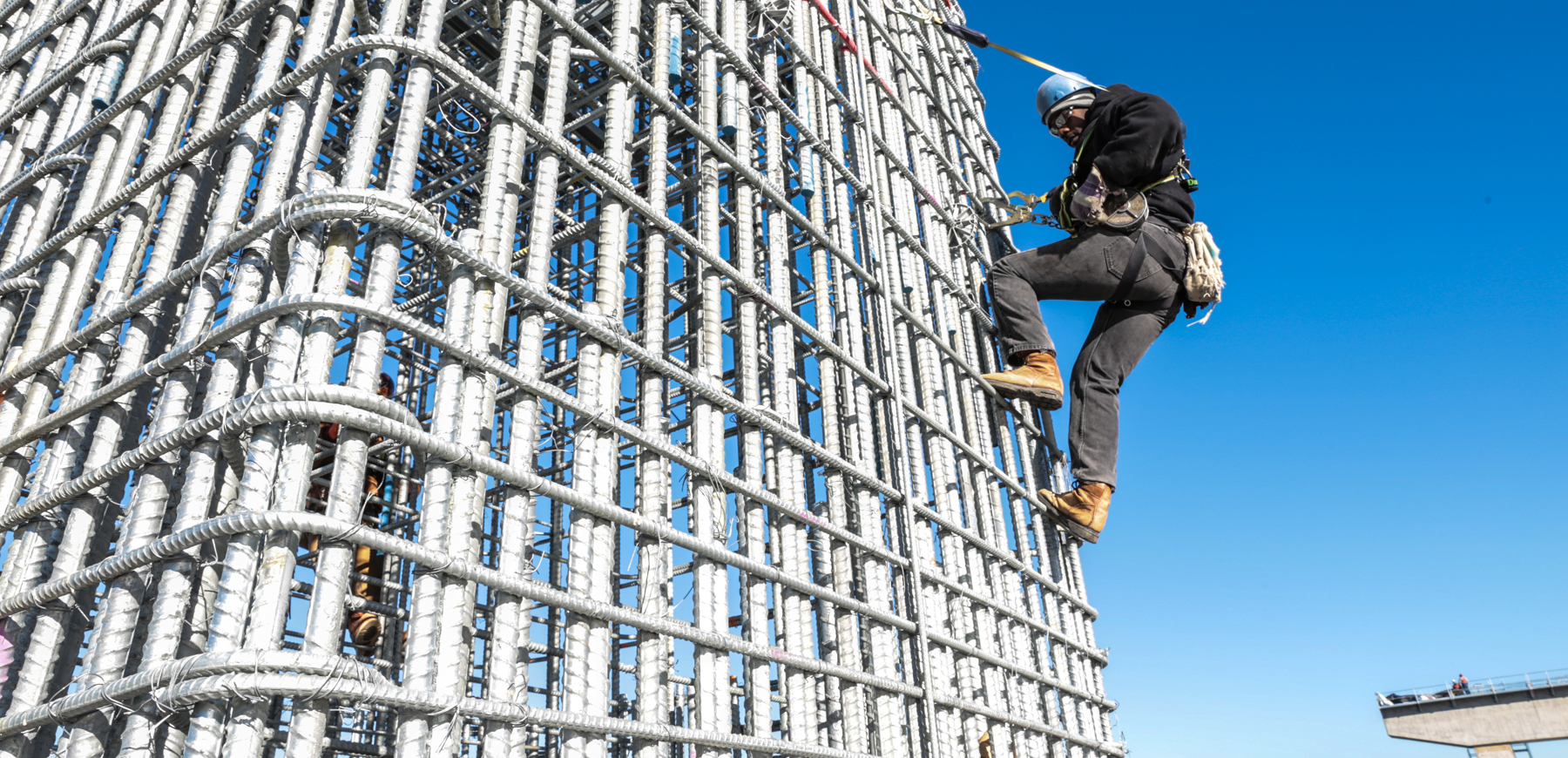
(Photo Credit: New York State Thruway Authority)
Field Handling Techniques: HDG vs. Fusion Bonded Epoxy-Coated
The galvanized coating uniquely provides both barrier and cathodic protection to the steel. First, galvanizing’s barrier protection is superior to other barrier coatings due to the formation of a metallurgical bond with the steel. Other barrier coatings, such as fusion-bonded epoxy (FBE), rely strictly on surface adhesion to the steel.
The following PDF details the field handling techniques that should be employed when installing either galvanized or fusion-bonded epoxy-coated reinforcement:
Field Handling Table: Hot-Dip Galvanizing vs. Fusion-Bonded Epoxy (AGA) (47 KB) (47 KB)
Bending Galvanized Rebar
CGR rebar can be formed after galvanizing in the same way as bare uncoated rebar. The pure zinc coating is more formable than the base steel, so the zinc coating does not restrict formability of the bar. CGR can be processed on automated rebar bending machines.
When bending HDG rebar after the hot-dip galvanizing process, some cracking or flaking of the galvanized coating at the bend may occur. The speed of which the article is bent also may affect the coating integrity. The galvanized coating is best maintained at slower bend speeds. Some cracking and flaking of the galvanized coating in the bend area is not cause for rejection. Any flaking or cracking can be repaired by an acceptable repair method (see Touch-up & Repair).
Usually when cracking or flaking of the coating occurs on the bent section of the rebar, corrosion protection is still available. Coating thickness measurements will indicate that the zinc-iron alloy layers are still intact to provide numerous years of corrosion protection.
If rebar will be bent before galvanizing, see recommendation on the Mechanical Properties page
Touch-up & Repair
Although galvanized coatings are highly abrasion resistant, coating damage may occur once the galvanized steel leaves the galvanizer’s facility due to extremely rough handling, installation techniques, or in-service conditions. There are methods available to ensure post-galvanizing coating integrity.
There are three widely available accepted touch-up and repair methods: zinc-rich paint, zinc-based solder, and zinc flame spray (metallizing).
Zinc-rich paint
Organic or inorganic zinc-rich paint for touching up and/or repairing galvanized steel should contain between 65-69% zinc by weight, or >92% by weight metallic zinc in dry film. Inorganic zinc-rich paints are more effective than organic in terms of delivering corrosion protection, and they do not shrink after drying/curing as organic coatings do. This is a major advantage when the paint is applied to corners, edges and rough surfaces.
Zinc-rich paint is brush- or spray-applied to a clean, dry steel surface. Spraying or brushing should be in a single application of multiple passes according to the paint manufacturer’s instructions. Zinc painting can be done on the job-site and is the easiest repair method to perform because limited equipment is required.
Zinc-based Solder
Soldering with zinc-based alloys consists of applying zinc alloy -in stick or powder form -to the area to be repaired, which has been preheated to approximately 600 F (315 C). Common repair solders include zinc-tin-lead, zinc-cadmium and zinc-tin-copper alloys.
The surface to be reconditioned shall be wire-brushed, lightly ground, or mild blast-cleaned. All weld flux and spatter must be removed by mechanical methods if wire brushing or light abrasive-blasting is inadequate. The cleaned area should be preheated to 600 F (315 C) and wire-brushed at the same time. Care must be taken to not burn the surrounding galvanized coating. When the repair has been completed, flux residue can be removed by water rinsing or wiping with a damp cloth.
Zinc Flame Spray (Metallizing)
Metallizing is the melting of zinc powder or zinc wire in a flame or electric arc and projecting the molten zinc droplets by air or gas onto the surface to be coated. The zinc used is nominally 99.5% pure or better. The performance of wire versus powder is comparable. Zinc-aluminum alloys also can be used. The application equipment used may limit the concentration of aluminum.